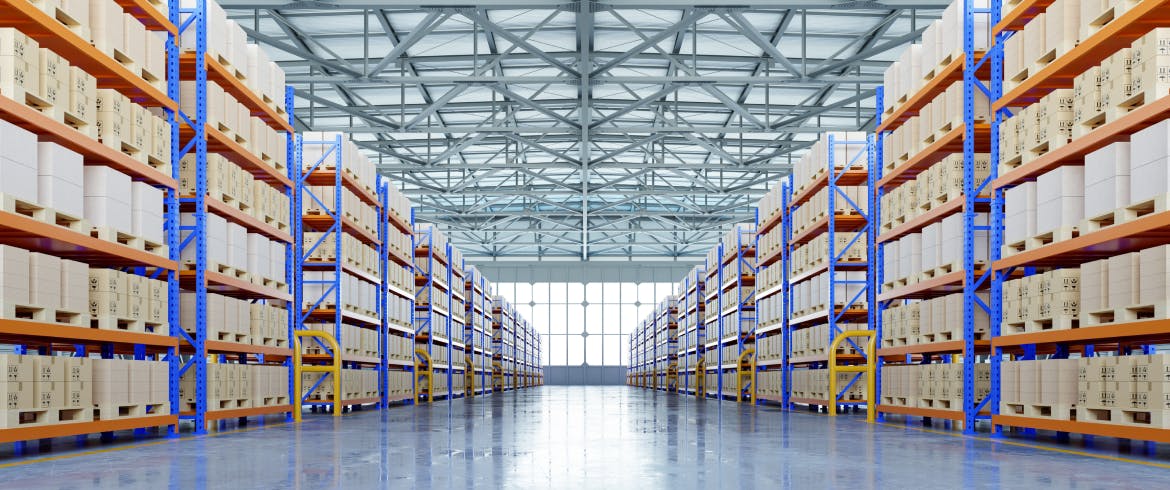
A Step-by-Step Guide of How to Measure the Cost of Delayed Routine Parts
This article was featured in the May 2023 edition of Aviation Week's digital magazine.
We are all aware of the problem of long lead times and routine parts delays, but how can we solve it? We must take a step back and take some advice from British mathematician Lord Kelvin.
He famously said, “If you cannot measure it, you can not improve it.” Therefore, let’s look into what data you should collect, what metrics you should be gauging, and explain the difference between direct and indirect costs.
Steps to Accurate Measurement
- Track Operational Downtime: This is important to measure because it’s the root cause of everything else that happens because of it. Track the total amount of operational downtime caused by delayed routine parts. This includes the time required to remove and replace components and any related costs, such as maintenance labor, aircraft ground time, and additional fuel burn.
- Monitor Flight Disruptions: This is where you can experience a significant impact, especially if you are a low-cost, short-haul carrier with a tight schedule. You should evaluate the impact of delayed routine parts on flight schedules by tracking the number of canceled or delayed flights and the associated costs, such as lost revenue, compensation for affected passengers, and damage to your reputation (which, of course, is less concrete to derive).
- Understand Inventory and Supply Chain Costs: This can also be described as the cost of solving the delayed parts problem. During moments of a disrupted supply chain, it’s common to mitigate risk by (over)stocking spare parts and/or paying for expedited delivery. All of these costs needed to be accounted for. These costs include the cost of warehousing and the opportunity cost of capital tied up in inventory, shipping fees, and overtime costs.
- Track Maintenance Costs: This is the most direct cost, and thus the one that is typically accounted for. These costs include the cost of maintenance labor and materials required to remove and replace components, as well as the cost of maintenance management time spent coordinating and monitoring deliveries.
- Monitor Aircraft Utilization: An aircraft only makes you money when it’s in the air; therefore, you need to know the number of aircraft that are grounded, taken out of service, or how your fleet utilization has been altered due to component failures or parts shortages.
Understanding Direct & Indirect Costs
Once you’re able to monitor and understand key metrics related to delayed parts, it’s important to know the distinction between direct and indirect costs.
Direct costs are the ones that come top of mind, and as the name suggests, are most closely related to your delays. Direct costs include:
- Increased Maintenance Costs: Maintenance delays of an aircraft for an extended period of time due to receiving a replacement part late can lead to increased labor and overhead costs, which add up quickly.
- Inventory Holding Costs: This includes having to carry an excessive amount of inventory to account for long lead times, which increases the costs associated with storage, insurance, and potential obsolescence.
- Lost Revenue: You lose revenue from the inability to operate the aircraft on time. As we previously stated, an aircraft on the ground is not making you any money but still equates to the same fixed cost.
In addition to these direct costs are indirect costs, which are caused by delayed parts and grounded aircraft. Indirect costs include:
- Reduced Customer Satisfaction: Long lead times can result in delays and cancellations, which can lead to unsatisfied customers who may look elsewhere for their next flight.
- Reputation Damage: Delays, cancellations, and safety concerns related to long lead times can harm the reputation of the airline and result in a loss of customer trust and confidence as well as negative press.
- Regulatory Penalties: You may face regulatory penalties if you are unable to comply with maintenance schedules, leading to additional costs and administrative headaches.
Long lead times for aviation parts can result in significant direct and indirect costs for airlines. These costs can have a negative impact on your bottom line and reputation, making it important for you to manage your supply chain effectively and reduce lead times wherever possible. This all begins with the proper monitoring and understanding of key metrics.
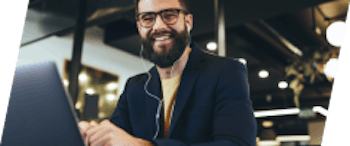
Choose the service level you currently need and scale up and down as needed. You'll pay for everything your aircraft material procurement process needs and nothing it doesn’t – no risky contracts and frivolous add-ons.