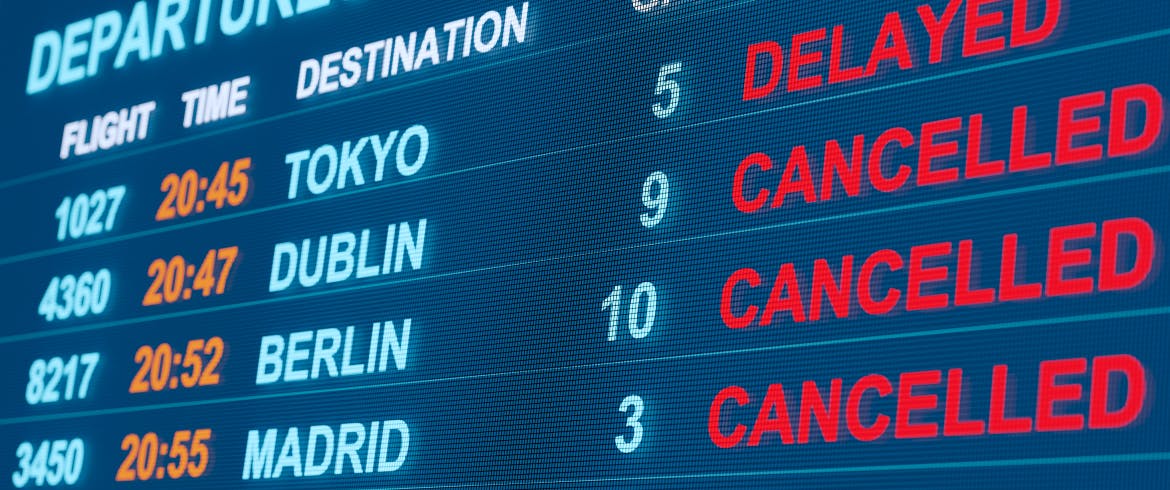
Inaccurate Information Leading to Massive Lead Times — Here’s What Can be Done
By Tulika Dayal, Chief Customer Officer at SkySelect.
In our digital era, information and data are the lifeblood of business. While we’re sitting on more information than ever before, that data often comes unstructured, incomplete and/or inaccurate.
Specifically, inaccurate and outdated catalogs are leading to long fill rates and reliability issues, disrupting the entire aviation supply chain.
Let’s delve deeper into the problem, and its impact and then look at how we can resolve it.
The Impact
On average, airlines face part delays of 60-90 days. Even routine parts are experiencing significant delays leading to AOG and Urgent situations. Some airlines have told us as much as 40% of AOG team’s demand stems from routine parts demand that couldn’t be delivered on time.
As you can imagine, these highly avoidable AOG disruptions can’t and shouldn’t happen. This risks Tech Ops from keeping the reliability of aircraft high and predictable. Then this trickles down all the way to the end traveler who is faced with delays or cancellations, reducing the airline’s all-important on-time performance (OTP).
Adding injury to insult to these delays are the additional costs associated with them. To accurately measure the cost of delayed routine parts for airlines on operations requires:
- tracking operational downtime,
- evaluating the impact on flight schedules,
- monitoring inventory and supply chain costs,
- tracking the impact on maintenance costs, and
- monitoring the impact on aircraft utilization.
For instance, the dire AOG situation leads to an increase of 40-60% for parts since the fix must be made urgently.
By regularly monitoring and tracking these costs, airlines can identify areas for improvement and implement strategies to minimize the impact of delayed routine parts on their operations.
The natural reaction to these long lead times and huge backlogs is for an airline to overstock parts and keep them on hand in the hangar. While this might be considered a means of hedging operational risk, in essence, all you are doing is trading one potential problem for another.
The issue with overstocking parts is that the strategy requires a large upfront amount of capital spend, which is very dangerous considering the razor-thin margins airlines are historically up against when running their business.
Most of the industry is still recovering from the effects of Covid and now navigating through an economic downturn, and airlines either cannot risk spending so much capital or simply don’t have the capital needed to properly overstock parts.
The Solution
So how can we alleviate this snowballing problem? Two letters — AI. I know what you might be thinking, but no, this isn’t the latest piece of content trying to hollowly latch on to a buzzword. As a matter of fact, artificial intelligence has been playing a role in the aviation supply chain long before the idea of ChatGPT was conceived.
Specifically, SkySelect's AI ensures that routine parts are delivered on time and at a good price point by using advanced algorithms running in the background. In order to do this, the maximum amount of quotes is collected automatically, ensuring that all business requirements are met, including lead times, part conditions, locations, shipping costs, and any other parameters that must be taken into account.
And when problems do arise, this is when the real magic of AI happens. When any kind of issues pop up that could cause order delays, the AI is programmed to resource a number of resolutions. For example, switching an order to urgent or resolving logistics complications.
It’s not just about making reactionary moves either. SkySelect’s AI has powerful forecasting features that enable airlines to see the trends of which parts are drying up in the market or have longer lead times and pre-stock the parts before the parts can impact the operations.
A multitude of data points is ingested to build an accurate forecast model, including historical consumption figures and current market metrics such as parts availability and costs. This way, airlines can not only keep up with the market but get and stay ahead of the game.
Long lead times for aviation parts can result in significant direct and indirect costs for airlines. These costs can have a negative impact on the airline's bottom line and reputation, making it important for airlines to manage their supply chain effectively and reduce lead times wherever possible.
We might find ourselves in a complicated supply chain, but by eliminating inaccurate or incomplete data and replacing them with accurate and complete models powered by AI, airlines can comfortably ride out the turbulent times of today’s economy and position themselves for a bright future.
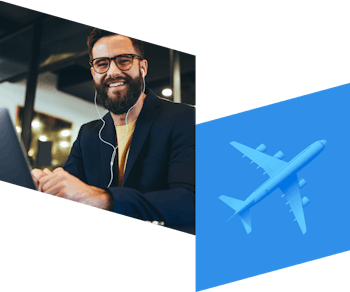
SkySelect's AI ensures that routine parts are delivered on time and at a good price point by using advanced algorithms running in the background.